TRACK 2, DAY 1
Using Anionic Polymer Gels To Achieve Maximum Turbidity Reduction From Construction Projects
ABSTRACT
Federal and state regulations have required construction projects to mitigate turbidity in discharge water for over three decades.
The negative impacts from offsite discharge of sediment include light extinction, oxygen reduction, habitat smothering, heavy metals, bacteria, pesticides, eutrophication, and fish kills.
Anionic polyacrylamide (PAM) technologies have evolved to meet this challenge. These PAMs are environmentally benign and are very adaptable for development project applications. The most recent delivery systems are capable of routinely reducing turbidity 80-90% or more at a cost-effective rate.
This presentation will compare various PAM mixing technologies that use polymer gel blocks as flocculant. These include ditch mixing systems, baffle grid systems, swirl tank systems, baffle tank treatments, and pipe mixing. Comparisons will be made regarding turbidity removal %, pre and post treatment turbidity, volume of water treated, and costs (when available).
Polymer treatment systems consist of five parts:
- Correct PAM blend matched to soil or water.
- Correct dosage.
- Reaction time.
- Properly designed mixing device for maximum polymer agitation.
- Particle capture system (dispersion field, particle capture system, jute baffles).
Mixing systems range from a simple ditch to engineered in-pipe mixing devices with venturi air injection.
All of these PAM mixing systems have demonstrated the ability to remove 80-90% of project turbidity. Some are capable of consistently removing 95% or more of sediment particles in water. All of them require rapid agitation to increase polymer interaction with target soil particulate.
Improved technology reduces the footprint of the treatment system and allows for more treatment volume than previously achieved.
The simplest system is a ditch mixing system. A trench is excavated, or materials are assembled to make a trench (hay bales, concrete blocks). Plastic is placed in the trench to contain water flow. Baffles or check dams are placed in the trench to add turbulent mixing during flow. Polymer blocks are placed at intervals (6-10 feet) to disperse PAM during water flow.
A jute particle capture system or dispersion field is added at the end of the ditch to capture soil agglomerations and PAM flocculant. Field adjustments are made to the location of the polymer blocks and number of baffles/check dams. This system can be used in either passive (gravity/runoff) treatment or active (pumped) treatment.
A baffle grid system is next in development stages for treatment. Ditch mixing systems are short-term items used for several days to weeks. Baffle grid systems are used for months and sometimes years. These can be used in passive or active treatment systems as well.
A large ditch is excavated to direct runoff to the baffle grid system. Often there is need for a grit pit to settle heavier sediments before polymer dosing. The ditch widens to a rectangular area where wooden baffles are constructed. These are often made of 2x4s and plywood to again allow for turbulent mixing with the polymer blocks.
Immediately downstream from the baffle system will be a series of rectangular 2×4 frames that are covered with jute, burlap, coconut, or other natural fiber material. This is where the particulate will attach to the material and clean water allowed to discharge.
Tank mixing and swirl mixing technologies use containers to agitate the polymer blocks. Tanks can be circular or similar to frac tanks. Pumped water is passed over polymer blocks and discharged through a series of particle capture curtains. The flow of water can be horizontal through weir tanks or vertical in the case of an upwell swirl tank. Clarified water is discharged offsite through a particle capture system or to a holding pond.
In-pipe mixing systems produce the maximum polymer mixing in the smallest technology footprint. Polymer blocks are reconfigured in a series of crimped links contained in a netting material. These links are placed inside of the dewatering pipes for polymer mixing. Instantaneous agitation can be achieved within these systems.
No baffles or check dams are needed as all mixing occurs within the pipe and hoses. This is then discharged through a particle curtain or tank containing capture materials. Flow rates of up to 300-5,000 gpm can be achieved in these systems.
Air-injection via venturi can be added to an in-pipe system. This additional component produces millions of ultra-fine bubbles which increase the agitation mixing of water and polymer, reducing treatment system size. This results in a treatment system that is the same size as a large ice chest, housing the pump, air injection system, and intake/discharge manifold.
PVC pipe is connected to these systems in adjustable lengths needed to reach the target water source. Particle capture is added to complete the process.
Particle capture can be accomplished using options which can be added or modified to meet site conditions. Several options are in use: particle capture curtains, dispersion fields, continuous particle curtains, and floc tanks. Each of these works best under different site conditions.
Gel-block PAM treatment systems produce consistent turbidity reduction in an economical, environmentally safe manner. These systems can be contractor assembled (with training) or can be turn-key rental/purchase units from select distributors. They are very flexible and adaptable technology for project management.
ABOUT THE PRESENTER
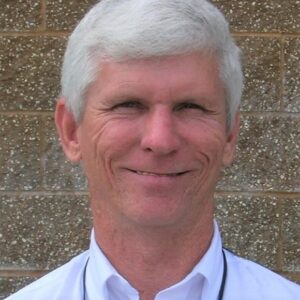
Eddie Snell, Applied Polymer Systems
Eddie Snell has over forty years of experience working in the watershed protection, erosion, sediment control, and stormwater industries.
Prior to working for Applied Polymer Systems, Inc, Eddie worked for the Walt Disney World Company and the Reedy Creek Improvement District (local government) in their environmental management division. He holds a four-year degree in Environmental Science.
Eddie has been an instructor for the Florida Stormwater, Erosion, and Sediment Control Inspector Training Program for over twenty-five years. He recently became a Certified Inspector of Sediment and Erosion Control practices (CISEC).
Eddie’s passion in life is the immediate and future protection of water resources.